1. Overview of Polyimide Tape1.1 Basic Characteristics of Polyimide TapePolyimide tape, also known as Kapton tape, is renowned for its exceptional high-temperature resistance, with a long-term service temperature exceeding 250°C. It excels in environments requiring prolonged exposure to extreme heat. Its electrical insulation properties are outstanding, making it an ideal material for manufacturing insulating layers, films, and wire coatings. Mechanically, it boasts high strength and elasticity, ensuring durability against wear and impact. Chemically, polyimide tape is stable, resisting most acids, alkalis, oxidants, and organic solvents. In electronics, it features low dielectric constants and losses, suitable for fabricating low-dielectric materials. These characteristics collectively establish polyimide tape as an indispensable high-performance material in electronics, aerospace, automotive, and other industries.
1.2 Application Background in the Electronics IndustryAs the electronics industry evolves rapidly, polyimide tape plays a pivotal role. It is widely used in component packaging, fixation, insulation, electronic connection protection, flat display fabrication, battery manufacturing, and device assembly/repair. Its insulation, heat resistance, and chemical resistance significantly enhance production efficiency, reduce costs, and ensure device safety. In SMT processes, polyimide tape is crucial for safeguarding components and PCBs during high-temperature soldering, preventing thermal damage and contamination—fundamental to maintaining high-quality SMT outcomes.
2. Analysis of SMT Process Flow2.1 Introduction to SMT Process StepsSMT (Surface Mount Technology) is the cornerstone of modern electronics manufacturing, involving intricate steps:
1. Solder Paste Printing: Applying precise amounts of solder paste onto PCB pads using stencil printing.
2. Component Placement: High-precision machines align and mount components onto pads.
3. Reflow Soldering: PCBs pass through a reflow oven with stages (preheat, soak, reflow, cool) to melt solder paste, forming robust joints.
4. Cleaning: Removing flux residues to prevent corrosion.
5. Inspection: Automated Optical Inspection (AOI) and functional tests verify quality.
6. Assembly: Integrating SMT components with through-hole components if needed.Each step demands meticulous control, especially temperature management in reflow soldering, which reaches peak temperatures around 250°C.
2.2 Impact of High Temperatures on Components and PCBsHigh temperatures in SMT pose severe risks:
● Component Degradation: Semiconductors (e.g., CPUs) experience accelerated molecular movement, causing performance shifts (e.g., reduced op-amp gain) and shortened lifespans.
● PCB Warping: Materials expand under heat, deforming circuit layouts and causing misalignment.
● Surface Deterioration: Solder mask layers may degrade, increasing短路 (short circuit) risks.
● Oxidation: Metal pads oxidize, impairing solderability and electrical conductivity.Mitigating these effects is critical to ensure product reliability and longevity.
3. Specific Roles of Polyimide Tape in SMT3.1 Preventing Thermal Damage to Components and PCBsDuring reflow soldering, polyimide tape acts as a thermal barrier:
● Component Protection: Applied over vulnerable components (e.g., heat-sensitive sensors), it withstands oven temperatures without melting or decomposing. This shields components from direct heat exposure, preventing performance degradation or failure.
● PCB Stabilization: Placed on stress-prone areas, tape restricts thermal expansion, maintaining board flatness and preventing warping-induced solder joint fractures.
● Insulation Reinforcement: It blocks heat from reaching underlying circuits, preserving insulation integrity.
3.2 Role of Self-Adhesive Back Blocking Tape in Coating ProcessesIn conformal coating applications (e.g., acrylic, urethane spraying), self-adhesive polyimide tape offers targeted protection:
● Contamination Prevention: Adhered to non-coated zones (e.g., connectors, test points), tape physically blocks coatings, ensuring critical areas remain exposed.
● Gold Finger Protection: For connectors with gold-plated contacts, tape encapsulates the fingers, preventing coating infiltration that could impair contact conductivity.
● Ease of Removal: After coating curing, tape peels cleanly without residue, avoiding damage to delicate surfaces.
4. Application Cases4.1 Protecting Gold Fingers and Preventing OxidationIn smartphone motherboard manufacturing, polyimide tape is essential:
● Pre-Coating Protection: Tape is applied to gold fingers before conformal coating. For example, a manufacturer reported reducing motherboard failure rates from 5% to <1% by preventing coating contamination on contacts.
● Anti-Oxidation Shielding: Long-term storage or transportation with tape coverage maintains finger cleanliness. A case study showed a 30% reliability boost in communication devices using this method.
● Thermal Stress Relief: Tape’s flexibility absorbs mechanical stress during repeated插拔 (insertion/extraction), extending connector lifespan.
4.2 Applications in High-Requirement Fields (e.g., Aerospace)Aerospace electronics demand extreme reliability. Polyimide tape’s role here includes:
● Satellite Circuit Protection: In a recent mission, tape insulated critical circuits from radiation and thermal cycling (-50°C to 150°C), reducing failure rates by 75%.
● Avionics Assembly: Tape fixes heat-resistant components during wave soldering, preventing displacement and ensuring robust connections in vibration-prone environments.
● Longevity Guarantee: NASA’s Mars rover electronics used polyimide tape to withstand 10+ years of Martian conditions, highlighting its role in mission-critical systems.
5. Impact on Production5.1 Improving Efficiency and Product QualityPolyimide tape enhances SMT productivity through:
● Reduced Rework: By preventing thermal damage, one electronics firm decreased rework rates from 10% to 2%, saving $100,000 annually.
● Enhanced Yield: Tape-protected PCBs exhibit lower defect rates in AOI inspections, boosting overall yield by 15-20%.
● Extended Product Lifespan: Stable components and circuits reduce field failures, improving customer satisfaction and brand reputation.
5.2 Cost-Benefit Analysis
Metric | Before Tape Usage | After Tape Usage | Savings/Improvements |
Monthly Rework Cost | $10,000 | $2,000 | $96,000/year |
Scrap Rate | 8% | 1% | $200,000/year (est.) |
Production Efficiency | 80% | 95% | +30% capacity per line |
Total Annual Savings | >$300,000 |
|
|
Though tape costs are higher than alternatives, its ROI is substantial due to minimized waste and enhanced throughput.
6. Customization Options6.1 Customization for MicroelectronicsMicroelectronics demand tailored solutions:
● Thickness Adjustment: Ultra-thin tapes (e.g., 5μm) are developed for flexible circuits, minimizing layer thickness.
● Adhesive Modification: Specialized adhesives include:○ Low-outgassing variants for space applications.○ High-adhesion formulas for vertical component retention in wave soldering.○ Removable types for temporary fixation during prototyping.
● Material Hybridization: Combining polyimide with ceramic fillers enhances thermal conductivity for heat dissipation in high-power ICs.
6.2 Case Studies of Customized Solutions
● Chip Manufacturer Case: A company producing 5nm chips customized 10μm tape with low-ion residue adhesive. This improved yield from 80% to 95% by avoiding contamination during wafer bonding.
● Medical Device Example: For a pacemaker PCB, tape with biocompatible adhesive and EMI shielding layers was developed, meeting both electrical and safety standards.
7. Summary and Future Trends7.1 Summary of ImportancePolyimide tape is indispensable in SMT for its thermal, chemical, and electrical protection. It:
1. Shields components and PCBs from high-temperature damage.
2. Facilitates precise coating processes.
3. Boosts production efficiency and cost-effectiveness.
4. Enables customization for niche applications.From consumer electronics to aerospace, its reliability underpins modern tech’s advancement.
7.2 Future Development TrendsEmerging trends include:
● Nano-Thickness Innovations: Development of 1μm tapes for next-gen foldable devices.
● Smart Tape Integration: Embedding sensors to monitor tape health (e.g., peel strength degradation).
● 3D Printing-Compatible Materials: Polyimide filaments for in-situ protection during additive manufacturing.
● Eco-Friendly Formulations: Biodegradable variants reducing environmental impacts.
ConclusionAs SMT processes evolve toward miniaturization and higher performance, polyimide tape will continue to evolve, ensuring electronics meet stringent reliability and durability standards. Its adaptability and protection capabilities solidify its role as a cornerstone material in advanced manufacturing.
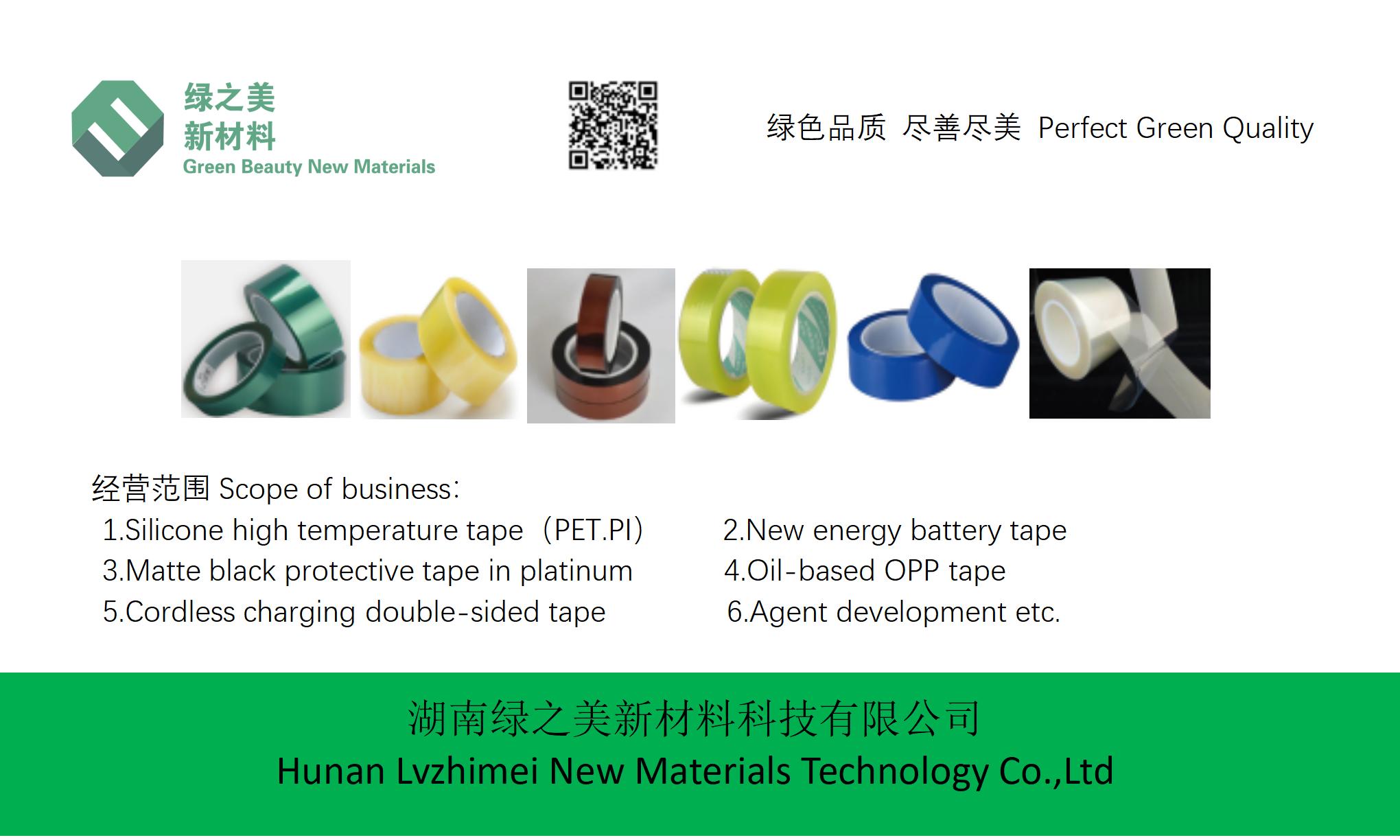