1. Introduction to Kapton Tape’s Basic Characteristics1.1 Composition and StructureKapton tape is primarily composed of polyimide, a high-molecular polymer containing imide rings in its main chain. It is synthesized through a two-step reaction involving diamines and dianhydrides. First, polyamic acid is formed through condensation polymerization in polar solvents, followed by thermal imidization to convert it into polyimide. The structure features highly stable and ordered molecular chains, imparting exceptional properties to the tape. During manufacturing, a polyimide film serves as the substrate, coated with high-performance silicone pressure-sensitive adhesive (PSA) and optionally laminated with a fluoroplastic release layer. This combination enhances processability and performance in electronics assembly applications.
1.2 Physical PropertiesKapton tape exhibits outstanding physical properties. Its thermal resistance is remarkable, withstanding temperatures up to 400°C for short periods and maintaining stability over -200°C to 300°C for long-term use. This makes it ideal for protecting components during wave soldering and thermal treatments. As an insulator, it has low dielectric constants and minimal dielectric losses, ensuring reliable electrical isolation. Chemically, it resists most solvents, acids, and alkalis, remaining intact during exposure to common cleaning agents or harsh environments. This durability directly contributes to product longevity and quality in electronics manufacturing.
2. Application Scenarios in Electronics Assembly2.1 Protection in Wave Soldering and Reflow SolderingDuring wave soldering, Kapton tape shields components from molten solder waves. When PCBs pass through the solder bath, exposed elements risk damage from high-temperature solder. By firmly adhering to targeted areas, Kapton tape prevents solder splashing and short circuits. Similarly, in reflow soldering, it protects delicate components or regions from thermal cycling, ensuring pins and connections remain intact. Case studies show its effectiveness in high-precision assemblies, boosting yield rates and reliability.
2.2 Role in High-Temperature ProcessesIn thermal treatments like aging tests or high-temperature environments (e.g., industrial control systems), Kapton tape acts as a thermal barrier. Its polyimide backbone maintains stability even at 400°C, preventing heat-induced deformation or performance degradation. For example, during equipment testing under extreme conditions, it encapsulates critical components to mitigate thermal stress, thereby extending device lifespan.
2.3 Fixation of Circuit Board ComponentsKapton tape offers versatile component fixation. It can be cut to precise shapes to secure irregular or sensitive parts, providing strong adhesion without conductive risks. Its insulative property prevents short circuits between components, while its flexibility accommodates board vibrations or mechanical stress. For instance, in aerospace electronics where lightweight and stability are crucial, tailored Kapton tape solutions ensure components remain fixed during rigorous operations.
3. Comparative Advantages Over Other Tapes3.1 Comparison with PET TapeThermal resistance differentiates Kapton tape from PET (polyethylene terephthalate) tape. While PET withstands up to 120-150°C, Kapton’s 400°C tolerance enables use in wave soldering and other high-temperature processes. Cost-wise, PET is more economical but sacrifices performance in extreme environments. Despite its higher price, Kapton’s long-term reliability reduces failures, offsetting costs over product lifecycles.
3.2 Comparison with Silicone TapeKapton tape surpasses silicone tape in insulation and chemical resistance. Polyimide’s lower dielectric constants enhance signal integrity in high-frequency applications. Additionally, while silicone tape may degrade when exposed to strong alkalis or hydrogen fluoride, Kapton’s inertness ensures stability across corrosive environments. This resilience makes Kapton indispensable in chemically aggressive assembly settings.
4. Protection of Gold Fingers with PI 300 Tape4.1 Function of Gold Fingers in Electronic DevicesGold fingers—gold-plated connectors on components like memory modules or expansion cards—are pivotal for electrical connections. Their superior conductivity, wear resistance, and oxidation immunity ensure stable data transmission. From gaming consoles to smartphones, gold fingers bridge circuits, enabling devices to function reliably. Any damage to these contacts risks signal loss or device failure.
4.2 Reasons for Using PI 300 TapePI 300 tape (a specialized Kapton variant) is chosen for gold finger protection due to its balanced adhesion, thermal resistance, and corrosion immunity. Its moderate tack allows easy application and removal without damaging delicate gold coatings. In flexible electronics or miniature devices, its thin profile and stability prevent interference with mating connectors, maintaining mechanical and electrical integrity.
4.3 Prevention of Corrosion and WearPI 300 tape acts as a barrier against environmental hazards. Its hydrophobicity and chemical inertness block moisture and corrosive gases, preventing oxidation. Mechanically, its smooth surface disperses friction during insertion/extraction cycles, reducing wear on gold plating. By combining protection against both environmental and mechanical stresses, PI 300 tape significantly extends the lifespan of connectors.
5. Thermal Performance Comparison of High-Temperature Tapes5.1 Temperature Range of Kapton TapeKapton tape’s operational range (-200°C to 300°C long-term, with short-term peaks up to 400°C) outmatches alternatives. This versatility enables its use in diverse thermal processes, from cryogenic testing to soldering. Its thermal stability is attributed to polyimide’s rigid molecular structure, which maintains integrity even under extreme conditions.
5.2 Thermal Limits of PET and Silicone TapesPET tape’s limit (120-150°C) restricts its use to lower-temperature tasks like temporary component fixation. Silicone tape, with a range of 200-260°C, suits moderate environments but fails in high-temperature soldering. Both materials soften or degrade beyond their thresholds, posing risks to assemblies.
5.3 Performance Advantages of Kapton Tape in High-Temperature EnvironmentsAt elevated temperatures, Kapton tape retains its mechanical strength, insulation properties, and chemical stability. For instance, in automotive electronics exposed to engine heat, it prevents wire harnesses from melting or short-circuiting. Its consistent performance under thermal cycling enhances product reliability, distinguishing it from lower-grade tapes.
6. Impact of Kapton Tape Thickness Selection on Electronics Assembly6.1 Insulation Performance of Thicker Kapton TapeThicker tapes (e.g., 0.1-0.2mm) offer superior insulation for high-voltage applications. Their increased dielectric thickness reduces current leakage risks in transformers or power electronics. However, thicker materials may require more force for application and limit flexibility on curved surfaces.
6.2 Handling and Adhesion of Thinner Kapton TapeThinner variants (e.g., 0.025-0.05mm) excel in precision assembly. They easily conform to intricate geometries without introducing air bubbles, ideal for SMT components or flexible circuits. Their lightweight nature also reduces stress on delicate substrates.
6.3 Thickness Selection for Specific ApplicationsOptimal thickness depends on the scenario:
● Wave soldering: 0.1mm for robust protection.
● Gold finger shielding: 0.05mm to avoid interference with connectors.
● Fine component fixation: 0.025mm for minimal profile.Balancing thickness with application requirements ensures both functionality and manufacturability.
7. Applications in Battery Encapsulation and Other Fields7.1 Synergistic Use with lvmeikapton Insulating Tape in Battery EncapsulationIn battery assembly, Kapton tape and lvmeikapton insulating tape collaborate for comprehensive protection. Kapton provides thermal stability during battery formation processes (e.g., high-temperature curing), while lvmeikapton reinforces electrical isolation between electrodes. This synergy enhances safety in lithium-ion batteries for EVs, ensuring cells withstand thermal abuse without short circuits.
7.2 Role of Kapton Tape in Battery EncapsulationKapton tape seals battery components (e.g., electrode tabs, separators) to resist thermal shrinkage and chemical corrosion. Its PSA adheres firmly to diverse battery materials without leaving residues. In pouch cells, it aids in dimensional stability during stacking, preventing deformation under pressure.
8. Summary and Future Outlook8.1 Core Advantages SummaryKapton tape’s strengths lie in its:
● Ultra-high thermal resistance (up to 400°C).
● Exceptional electrical insulation.
● Versatility in thicknesses and applications.From soldering protection to battery encapsulation, its performance boosts electronics reliability and lifespan.
8.2 Future Application ProspectsAs electronics evolve toward miniaturization and high-performance requirements, Kapton tape’s role will expand. In 5G infrastructure, its thermal stability supports heat-intensive components. Wearable devices benefit from its thin profiles and durability. Additionally, emerging technologies like flexible displays or aerospace electronics may drive demand for advanced Kapton formulations, solidifying its position as a cornerstone material in modern assembly.
ConclusionKapton tape’s unique combination of properties makes it indispensable in electronics assembly. Its ability to withstand extreme conditions while maintaining electrical and mechanical integrity ensures devices meet stringent quality standards. As industry demands escalate, Kapton tape will continue to evolve, enabling the next generation of reliable and innovative electronic systems.
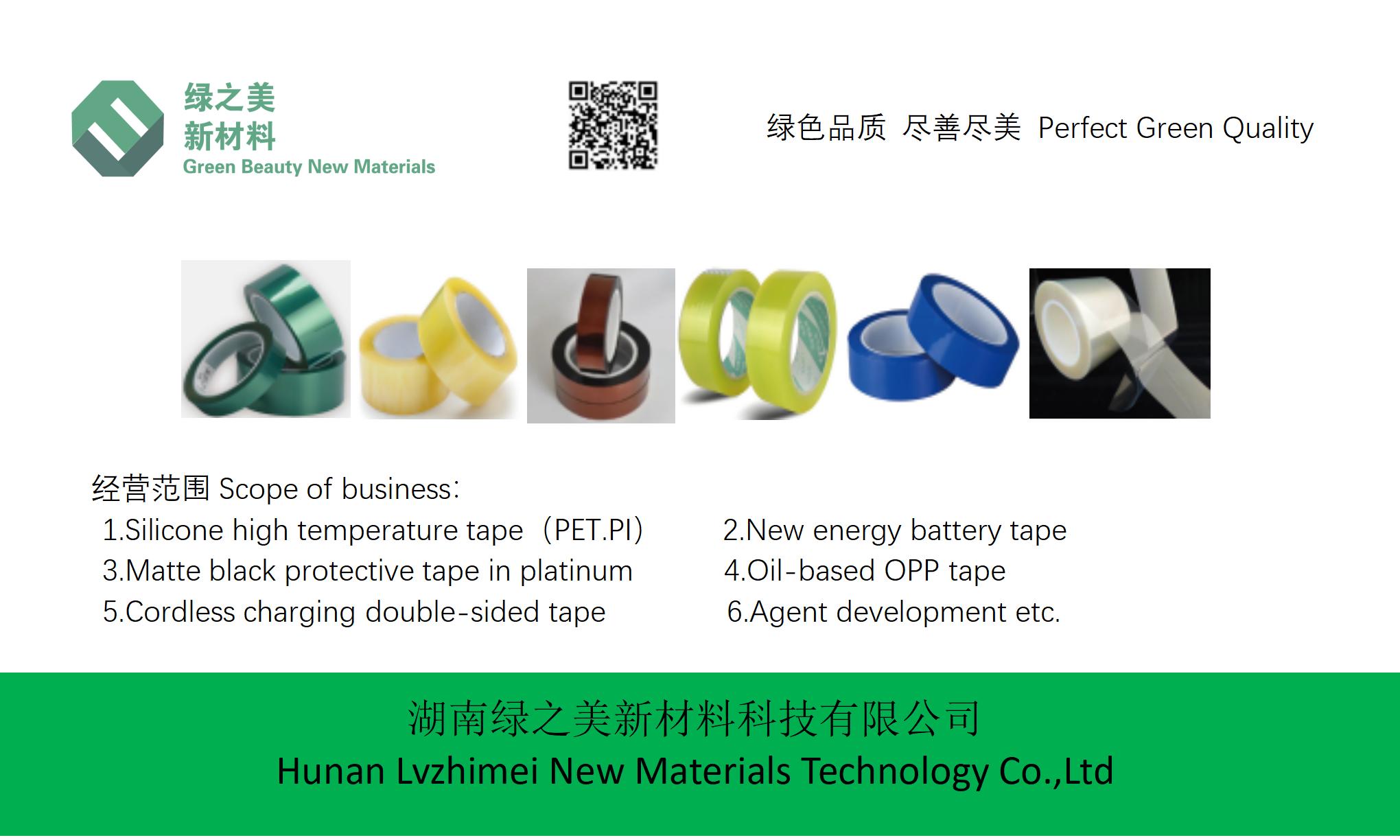