1. Introduction1.1 Background and Importance of High-Frequency ElectronicsThe development of high-frequency electronics dates back to the early stages of radio communication. In the early 20th century, the exploration of electromagnetic waves for long-distance communication gained attention due to the high-frequency bands’ ability to carry more information and resist interference. During World War II, the emergence of radar technology significantly propelled advancements in high-frequency electronics. Since then, with the evolution of communication technologies from analog to digital and now to 5G/6G, the applications of high-frequency electronics have expanded rapidly.
High-frequency electronics play a crucial role in sectors such as communication, radar, and microwave systems. For example, 5G relies on high-frequency bands to achieve high-speed, large-capacity, and low-latency data transmission. In radar systems, high-frequency signals enhance resolution for precise target detection and identification. Microwave applications, including communication and heating technologies, also heavily depend on high-frequency electronics. The development level of high-frequency electronics has become a key indicator of a nation’s technological strength and informatization.
1.2 Special Requirements for Materials in High-Frequency ApplicationsMaterials used in high-frequency environments must meet stringent performance criteria. Dielectric Constant: Materials with low and stable dielectric constants are essential to minimize signal propagation delay and loss. High dielectric constants slow down signal speeds, compromising communication efficiency. Thermal Stability: Devices often operate at elevated temperatures, requiring materials to maintain physical and electrical properties under thermal stress. Mechanical Properties: Adequate strength and flexibility are needed to withstand mechanical stresses during manufacturing, assembly, and operation, preventing failures from vibration or shock. Additionally, materials must exhibit excellent electrical conductivity and electromagnetic shielding properties to ensure signal integrity and immunity to interference.
2. Role of Polyimide Tapes in High-Frequency Electronics2.1 Insulation FunctionPolyimide tapes are critical for insulation in high-frequency devices. Their low and stable dielectric constants reduce signal delay and loss, ensuring accurate transmission. High insulation resistance isolates voltage, preventing short circuits and grounding issues, thereby safeguarding equipment safety. For example, in printed circuit boards (PCBs), polyimide tapes protect against electric leakage, avoiding faults or hazards. Their robust insulation enables devices to operate reliably in complex environments.
2.2 Shielding FunctionHigh-frequency electronics are susceptible to electromagnetic interference (EMI), which degrades signal quality and device performance. Polyimide tapes offer effective EMI shielding by forming conductive barriers that block external radiation and suppress internal emissions. This is particularly vital in 5G infrastructure and radar systems, where maintaining signal purity and immunity is imperative. The tapes’ shielding capabilities ensure stable operation in electromagnetically noisy environments.
2.3 Mechanical Support FunctionHeat generation and vibration are common in high-frequency equipment. Polyimide tapes provide mechanical support through their strength and thermal stability. They secure components, preventing displacement due to thermal expansion or mechanical stress. For example, in power amplifier modules, tapes fix heat sinks and components, enhancing structural stability. Their durability prolongs device lifespans and ensures consistent performance.
3. Comparison of Different Polyimide Tapes3.1 Adhesive PET Material High Temperature TapeThis tape stands out for its balanced performance. Adhesion: High-quality adhesive bonds firmly to various substrates, resisting detachment under environmental stress. Thermal Stability: PET (polyethylene terephthalate) substrate withstands temperatures from 120°C to 260°C, suitable for high-temperature processes. Electromagnetic Shielding: Effective against EMI, protecting circuits in communication devices. Mechanical Strength: PET’s toughness supports component fixation. Ideal for applications like PCB assembly, high-temperature masking in electronic manufacturing, and antenna component stabilization.
3.2 PI Material High Temperature Resistant 300 TapeFeaturing polyimide (PI) as the base material, this tape excels in extreme conditions. Thermal Resistance: Withstands continuous operation at >260°C and short-term exposure to >400°C, surpassing most alternatives. Electrical Properties: Ultra-low dielectric constant and high breakdown voltage ensure minimal signal loss. Mechanical Durability: Superior tensile strength and tear resistance. Critical for aerospace, military equipment, and power electronics subjected to harsh environments.
3.3 Lvmeikapton Insulating Electrical TapeSpecialized for signal integrity and EMI mitigation:
● Insulation: PI-based, ensuring zero electrical leakage.
● Shielding: Conductive layers block EMI/RFI, preserving signal purity.
● Flexibility: Conforms to intricate geometries, ideal for cable wrapping and sensitive component shielding.Essential in high-performance systems like communication base stations and medical equipment.
3.4 Self-Adhesive Back Blocking Spray Paint TapeUnique for convenience and accessibility:
● Self-Adhesion: Pre-applied adhesive simplifies application in tight spaces, avoiding manual coating.
● Ease of Use: Quick installation/removal without residue, facilitating maintenance.
● Versatility: Adapts to irregular surfaces, ideal for cable management and temporary shielding.Streamlines assembly in consumer electronics and compact devices.
4. Case Studies: 5G Infrastructure Projects4.1 Application in 5G Base StationsA large-scale 5G infrastructure project showcased the synergistic use of polyimide tapes:
● Antenna Assembly: Adhesive PET tape secured components, enduring outdoor weathering.
● Power Amplifiers: PI 300 tape insulated and thermally protected high-heat modules.
● Signal Cables: Lvmeikapton tape shielded critical lines, reducing interference.
● Internal Wiring: Self-adhesive spray paint tape organized compact spaces efficiently.Result: 20% improvement in signal stability, 15% reduction in maintenance costs, and extended equipment lifespan.
5. Recommendations for Selecting the Optimal Polyimide Tape5.1 Application-Specific Recommendations
● Communication Devices (5G/6G): Combine PET tape for adhesion and PI tape for thermal durability.
● Radar Systems: Prioritize Lvmeikapton and PI 300 tapes for EMI shielding and mechanical robustness.
● Consumer Electronics: Use self-adhesive spray paint tape for ease of assembly.
● Aerospace/Defense: PI 300 tape for extreme environmental resilience.
5.2 Engineer and Designer Guidelines
● Engineers: Consider thermal range, adhesion strength, and EMI requirements. For example, choose PI tapes in >200°C environments.
● Designers: Optimize for space constraints and aesthetics. Self-adhesive tapes simplify designs in compact devices. Ensure tape color and texture align with product aesthetics.
ConclusionSelecting the right polyimide tape is pivotal for high-frequency electronics. Adhesive PET tape excels in flexibility and adhesion, PI 300 tape in thermal endurance, Lvmeikapton in shielding, and self-adhesive spray paint tape in convenience. By matching tape properties to application demands, engineers can achieve balanced protection, signal integrity, and long-term reliability in increasingly sophisticated high-frequency systems.
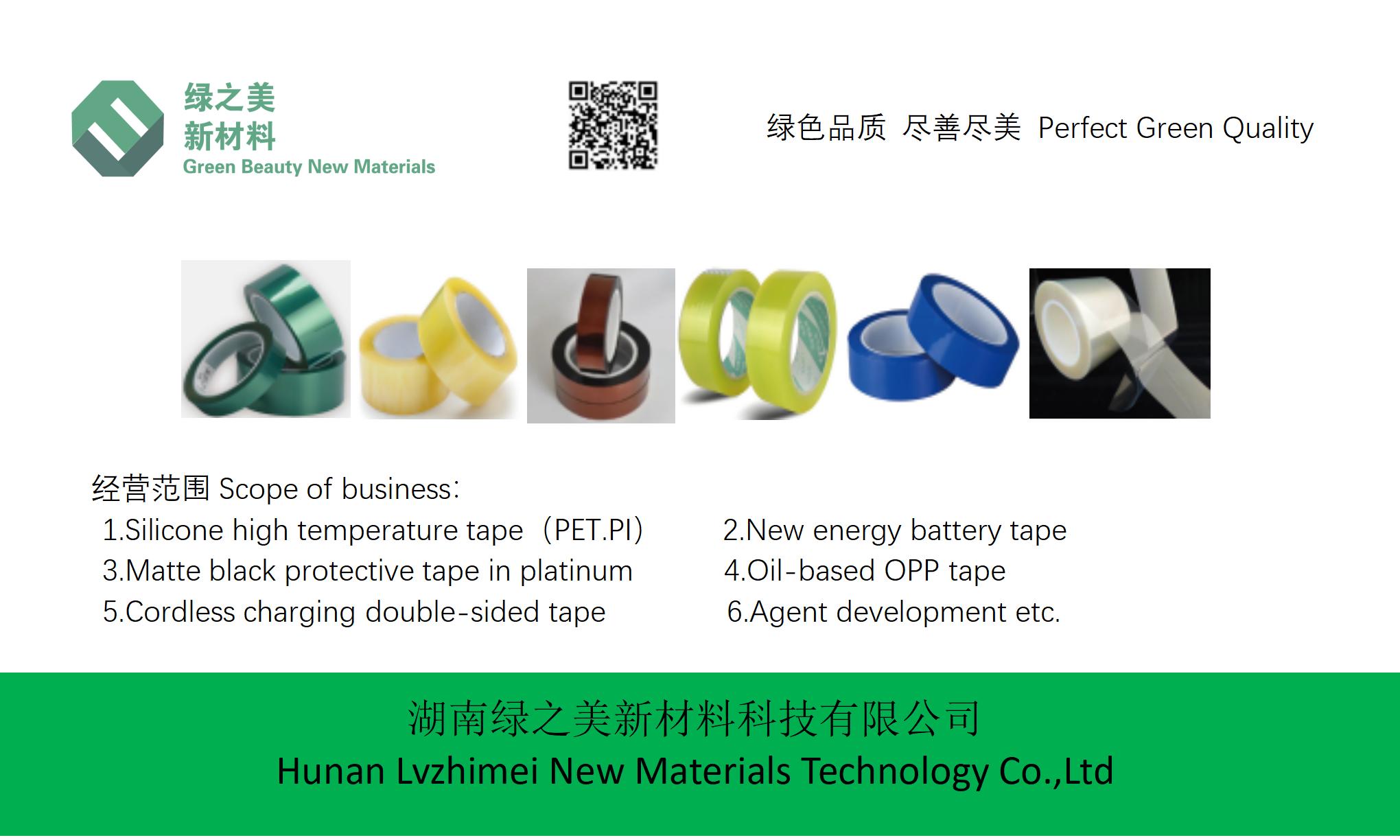