1. Introduction1.1 Definition and Overview of High Temperature TapeHigh temperature tape, as its name suggests, is an adhesive tape designed for use in high-temperature environments. It consists of a substrate and adhesive layer, with common substrates including polyimide film (PI), polytetrafluoroethylene (PTFE), and acrylic or silicone-based adhesives. This tape plays a crucial role in various industries due to its exceptional temperature resistance.
In electronic manufacturing, high temperature tape is indispensable. Processes like soldering, painting, and coating often require high temperatures, posing risks to electronic components. The tape provides protection, preventing damage and ensuring manufacturing stability. It also aids in circuit board insulation and shielding, enhancing product reliability. As a fundamental material in electronics, high temperature tape significantly contributes to product stability and longevity.
2. Key Features and Advantages of Brown Circuit Board High Temperature Tape2.1 High Temperature Resistance PerformanceBrown circuit board high temperature tape excels in temperature resistance, with common tapes enduring 120°C to 260°C, while advanced variants surpass 300°C. During wave soldering or engine compartment exposure, the tape maintains stability without melting, deforming, or deteriorating. This resilience ensures protection for sensitive components in automotive electronics and other high-heat scenarios.
2.2 Unique Insulation and Adhesion PropertiesThis tape offers superior insulation, preventing current leakage and withstanding high voltages, crucial for safety in communication devices and medical equipment. Its adhesion properties ensure secure bonding to circuit boards, even after thermal exposure. Unlike plastic tapes that may lose adhesion under heat or metal tapes that are costly and rigid, brown high temperature tape balances cost-effectiveness, insulation, and adherence.
3. Necessity of High Temperature Tape in Wave Soldering3.1 Potential Risks to Electronic Components in Wave SolderingWave soldering, a critical mass-production technique for through-hole components, exposes electronics to extreme heat. Lead-free soldering temperatures (e.g., Sn-Cu alloys at 260°C) can damage heat-sensitive components, while flux agents may corrode pins or surfaces, leading to shorts or poor connections. Design flaws like small pad间距 or improper fixtures can further increase defects.
3.2 Protection Mechanism of High Temperature TapeBy covering vulnerable components, the tape acts as a thermal barrier, shielding them from molten solder and corrosive flux. Without tape protection, components risk overheating damage, flux corrosion, and increased defect rates, compromising product functionality and reliability.
4. Application of High Temperature Tape in Thermal Management4.1 Impact on Heat Conduction and RadiationIn thermal management, high temperature tape containing导热 fillers enhances heat transfer efficiency by filling air gaps between components and heat sinks. For example, in LED lighting, the tape facilitates rapid heat dissipation from chips to sinks, prolonging LED lifespan. Its color (e.g., brown) may absorb or reflect radiation, mitigating thermal fluctuations.
4.2 Case Studies in Heat Dissipation DesignIn high-performance CPUs, adding high-temperature tape between the chip and heat spreader reduced peak temperatures by 5°C under heavy loads, stabilizing system performance and preventing thermal throttling.
5. Industry-Specific Applications5.1 Automotive ElectronicsIn engine compartments, brown tape insulates sensors and ECUs from heat, oil, and vibrations, ensuring engine control systems function reliably. It also protects wiring harnesses from corrosion, reducing electrical failures.
5.2 Aerospace and AviationCritical aerospace components, subjected to intense heat during flight, rely on high-temperature tape for structural reinforcement and insulation. For instance, tape on carbon fiber composites prevents thermal-induced delamination in aircraft wings.
5.3 Medical Device ManufacturingDuring sterilization cycles (e.g., autoclaving), tape protects internal electronics in devices like ultrasonic probes. It also aids in assembly by securing components during thermal curing processes.
6. Comparison with Polyimide Tape6.1 Temperature Resistance DifferencesWhile standard high temperature tapes withstand up to 300°C, polyimide (Kapton) tapes offer superior performance, maintaining stability at temperatures exceeding 400°C. This makes Kapton ideal for aerospace and high-end semiconductor applications.
6.2 Insulation Performance ComparisonPolyimide tapes exhibit higher dielectric strength and resistance, crucial in high-voltage environments. Their low dielectric loss ensures stable signals in advanced electronics.
6.3 Distinguishing Application ScenariosHigh temperature tapes suit cost-effective protection in automotive and consumer electronics, while polyimide tapes dominate aerospace, military, and medical devices demanding extreme performance.
7. Usage Methods and Precautions7.1 Ensuring Adhesion in High TemperaturesSelect tapes with suitable substrates (e.g., PTFE-coated glass fiber for non-stick properties). Ensure surfaces are clean and free of contaminants. Apply even pressure during installation, avoiding bubbles. For critical applications, use double-component adhesives and ensure proper curing.
7.2 Surface Preparation Before ApplicationThoroughly clean surfaces with solvents like isopropyl alcohol to remove oils and oxides. Sand or abrade surfaces to enhance adhesion, particularly for metals. For plastics, consider plasma treatment to improve bonding.
7.3 Common Mistakes and PreventionAvoid mismatching tape temperatures to application environments. Incorrect storage (e.g., exposure to moisture) can degrade performance. Ensure tape edges are cut straight to prevent unraveling.
8. Protection Effectiveness for Electronic Components8.1 Preventing Deformation and DamageDuring processes like reflow soldering, tape prevents components from warping or cracking due to thermal stress. For instance, in stepped-board manufacturing, tape shields exposed pads from contamination, maintaining solderability.
8.2 Long-Term Protection in Extreme EnvironmentsTests demonstrate tapes maintaining adhesion and insulation at 125°C for over 92 hours. In automotive applications, this ensures engine sensors function reliably over years of exposure.
8.3 Experimental and Case EvidenceA study showed tape-protected thermocouples accurately measuring temperatures during prolonged thermal cycling, validating its stability.
9. Chemical Resistance and Solvent Tolerance9.1 Resistance to Common Organic SolventsPI-based tapes resist toluene and acetone but may degrade in strong polar solvents like dimethylformamide. PTFE tapes offer broader resistance, suitable for harsh chemical environments.
9.2 Selection in Corrosive EnvironmentsIn acid-laden environments, PTFE tapes are preferred. For alkaline conditions, specially treated PI variants may be suitable. Always reference chemical compatibility charts.
9.3 Real-World Chemical Resistance CasesIn a chemical plant, PTFE tape protected circuits from acid vapor corrosion, preventing equipment failures. In pharmaceutical manufacturing, tape insulated heating elements from reactive solvents, ensuring process safety.
10. Impact of Tape Color10.1 Advantages of Brown Color in Visual InspectionBrown tape contrasts with circuit board components, aiding technicians in identifying covered areas during quality checks. Its visibility in dim environments reduces inspection errors.
10.2 Color Influence on Temperature ResistanceColor primarily affects heat absorption. Brown absorbs more heat than lighter colors, but this difference is minimal within tape’s rated temperature range.
10.3 Applicable Scenarios by ColorBrown: General electronics, automotive.Clear/Translucent: Optimal for visualizing underlying components.Black: Light-sensitive applications to absorb stray light.
11. Conclusion11.1 Summary of Applicable ScenariosBrown circuit board high temperature tape is essential in wave soldering, thermal protection, automotive electronics, aerospace, and medical devices. Its versatility and cost-effectiveness make it a cornerstone in high-temperature environments.
11.2 Emphasizing the Importance of High Temperature TapeIn industries where reliability is non-negotiable, tape prevents component failures, thermal degradation, and costly recalls. As electronic systems grow more complex, its role in ensuring longevity and safety becomes increasingly vital.
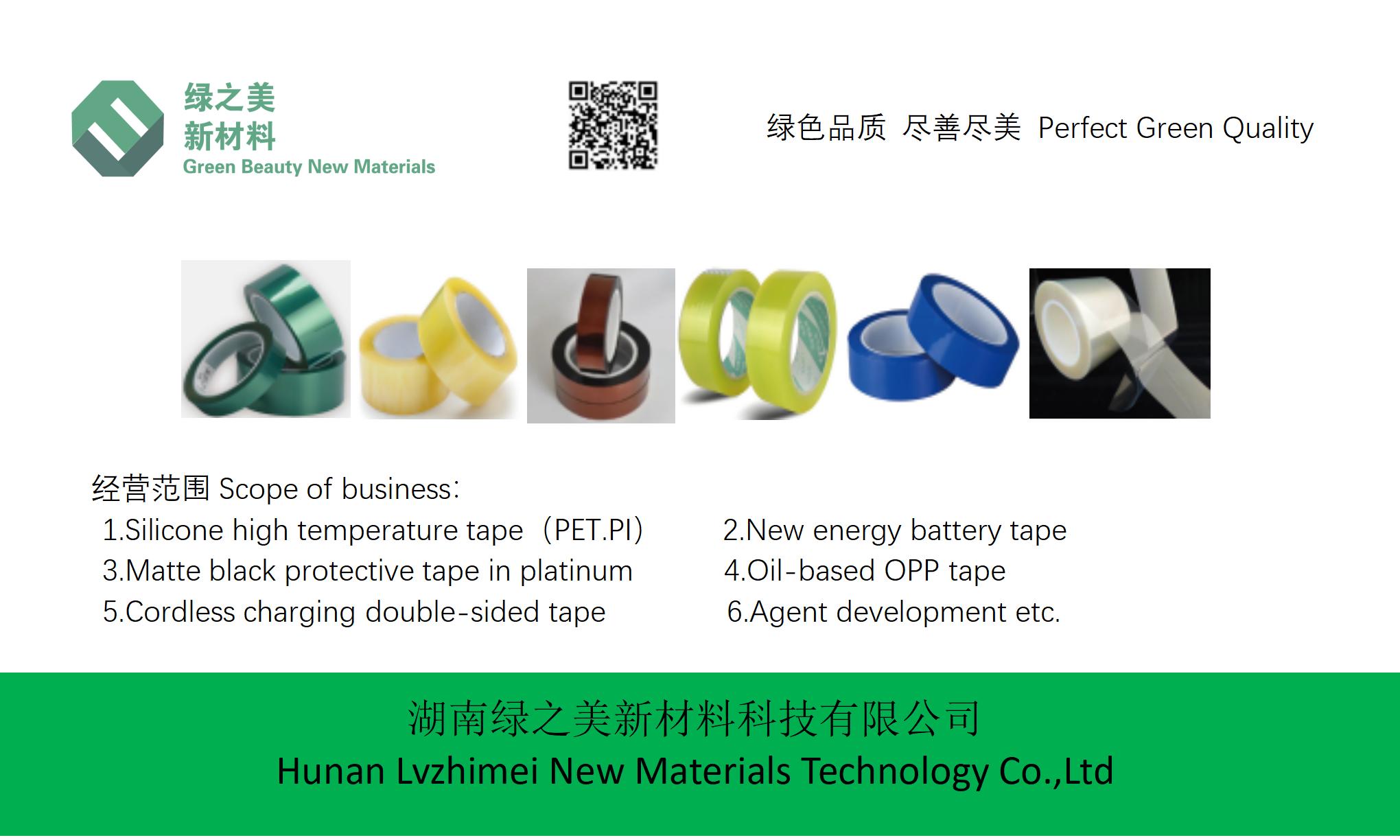