1. Key Characteristics of Kapton Tape
1.1 High-Temperature ResistanceKapton tape, made from polyimide film, exhibits exceptional performance in high-temperature environments. While ordinary tapes soften or melt at temperatures above 200°C, Kapton tape remains stable. It maintains physical and chemical properties up to 300°C, ensuring reliable insulation and adhesion.
Key Applications:
● Motor Manufacturing: Insulating H-class motor and transformer windings. High heat generated during operation requires Kapton tape to prevent short circuits.
● Electronics: Securing flexible printed circuits (FPCs) and electronic components in devices that operate under prolonged heat.
● Automotive Industry: Fixing engine components where temperatures exceed 150°C, enhancing reliability.
1.2 Electrical Insulation PerformanceKapton tape excels in high-voltage and high-frequency environments. Its high volume resistivity and surface resistivity effectively block current leakage. For example, in power transformers, it withstands strong electric fields to prevent breakdowns.
Advantages:
● Low Dielectric Constant and Loss: Ideal for high-frequency circuits to minimize signal attenuation.
● Stability in HV Environments: Essential for DC ultra-high voltage equipment insulation systems.
● PCB Protection: Shields components from interference and short circuits.
1.3 Chemical StabilityThis tape resists corrosion from acids, alkalis, and organic solvents (e.g., acetone, alcohol). Unlike PET tape, which may degrade in aggressive chemicals, Kapton maintains integrity.
Critical Uses:
● Li-ion Battery Manufacturing: Replacing chemically unstable PET tapes to prevent electrolyte reactions.
● Aerospace and Chemical Plants: Sealing pipelines and valves exposed to corrosive substances.
● Medical Devices: Withstanding sterilization processes involving harsh chemicals.
2. Key Factors Affecting Kapton Tape Selection
2.1 Temperature RequirementsDifferent Kapton grades cater to specific temperature ranges:
● <200°C: General electronics, consumer devices (standard Kapton tape).
● 200°C–300°C: Automotive engines, industrial equipment (high-temperature reinforced tape).
● >300°C: Specialized industrial processes (e.g., "PI material high temperature resistant 300 tape").
Selection Tips:Match tape type to peak operating temperatures to avoid premature aging or failure.
2.2 Adhesion NeedsTwo main types:
● Self-Adhesive: Coated with silicone pressure-sensitive adhesive for quick application (e.g., "Self-adhesive back blocking spray paint tape"). Ideal for flexible circuits or temporary fixes.
● Non-Adhesive: Requires additional bonding methods (e.g., thermal pressing) for high-reliability applications.
Adhesive Selection by Material:
● Metals: Epoxy for strong bonds.
● Plastics/Rubbers: Polyurethane for compatibility.
2.3 Electrical Insulation RequirementsIn high-voltage systems (e.g., >10 kV), prioritize tapes with:
● High breakdown voltage.
● Low moisture absorption to prevent conductivity.
● Stable performance under thermal cycling.
Example: "Lvmeikapton insulating electrical tape" is designed for substations, ensuring safety against arcing and corona discharge.
3. Application Cases in Various Industries
3.1 Electronics and Circuits
● PCB Protection: Shielding against abrasion during handling.
● Flexible Circuits: Enabling repeated bending without signal loss.
● Battery Insulation: Separating electrodes to prevent short circuits and chemical reactions.
3.2 Automotive Manufacturing
● Wire Harnesses: Insulating bundles exposed to engine heat, vibration, and oils.
● Sensors: Sealing against moisture and electromagnetic interference.
● Module Assemblies: Securing electronics under the hood.
3.3 Aerospace and Aviation
● Avionic Systems: Insulating wiring in high-altitude temperature extremes (-55°C to +200°C).
● Satellite Components: Lightweight insulation resisting radiation and vacuum conditions.
● Thermal Management: Wrapping heat-resistant cables near jet engines.
3.4 Medical and Biomedical Engineering
● High-Temperature Sterilization: Securing equipment during autoclaving (e.g., MRI components).
● Biocompatible Insulation: Implantable devices requiring non-toxic materials.
● Sensor Encapsulation: Protecting wearable health monitors from sweat and chemicals.
4. Comparison with PET Tape
4.1 Temperature Resistance
● Kapton: Up to 300°C (short-term 400°C).
● PET: Max 120°C (softens at 80°C+).
Consequence: Using PET in motor windings at 200°C leads to melting and insulation failure.
4.2 Mechanical Properties
● Kapton: High tensile strength, flexibility (ideal for dynamic environments).
● PET: Less durable; prone to cracking under stress.
4.3 Electrical Insulation
● Kapton: Superior dielectric strength (kV/mm) and long-term HV stability.
● PET: Adequate for low-voltage but risks breakdown in high-energy systems.
4.4 Cost Considerations
● Kapton: Premium price due to material and production complexity.
● PET: Economical for non-critical applications.
5. Case Studies: Consequences of Incorrect Selection
Case 1: Motor ManufacturerA company substituted Kapton tape with PET for H-class motor windings to save costs. PET melted at operating temperatures, causing short circuits and $500k equipment damage.
Case 2: Flexible Circuit FailureUsing a standard Kapton tape in a folding device led to adhesive delamination after 1,000 cycles, resulting in product recalls.
Lesson: Match tape properties precisely to application demands to avoid costly failures.
6. Comparison Table of Kapton Tape Types
Characteristic | Tape Type | Temperature Range | Adhesion Type | Key Features |
Basic Grade | Standard Kapton | <200°C | Self/Non-adhesive | Cost-effective for general electronics. |
High-Temp Grade | PI Material 260 Tape | 200–260°C | Reinforced Adhesive | Automotive engine wire insulation. |
Extreme Grade | PI HT-300 Tape | >300°C | Special Coating | Furnace gasketing, aerospace. |
Specialized | Self-Adhesive Blocking Tape | Varied | Silicone PSA | Spray painting masking (quick peel). |
Electrical Grade | Lvmeikapton Insulation Tape | Up to 220°C | Non-adhesive | Ultra-high voltage transformers. |
ConclusionSelecting Kapton tape requires assessing temperature exposure, adhesion requirements, and electrical stress. Matching these factors to application specifics ensures durability, safety, and cost-effectiveness. Avoiding substitutions (e.g., PET for Kapton) in critical environments is essential to prevent failures.
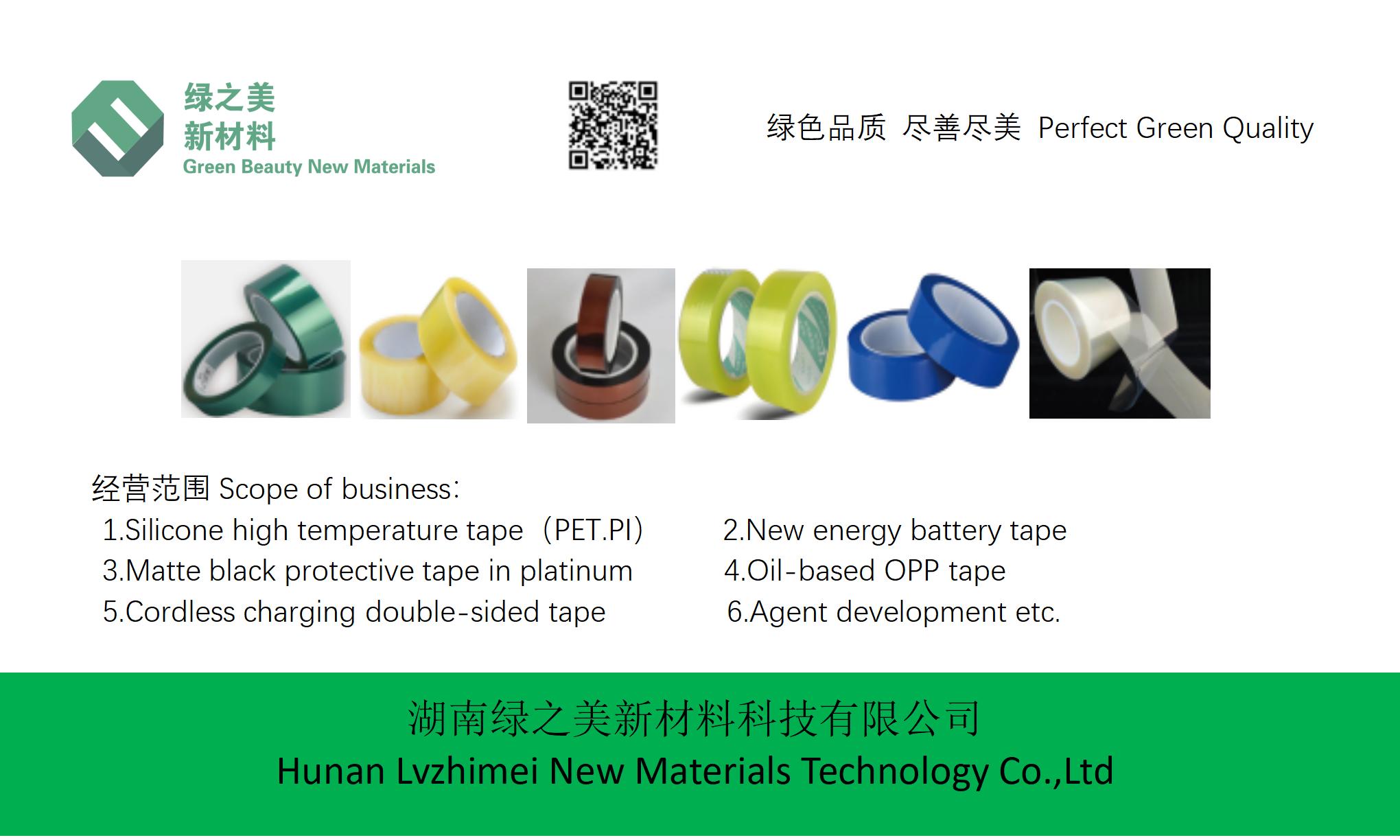